Many industries have undergone Digital Transformation processes, unlocking efficiencies and business benefits. Industrial environments are one such example, with IoT solutions now commonplace. But it’s important that organisations identify and leverage tools that will provide detailed insights from these technologies. Harshad Pingle, Product Manager for MindSphere, the industrial IoT as a service solution from Siemens, highlights the importance of putting industrial IoT data in context, as well as how businesses can take immediate steps to begin seeing results.
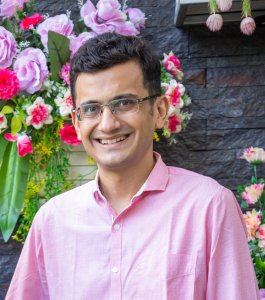
Operations Insight (OI) is a MindSphere solution designed to enable businesses to contextualise industrial Internet of Things (IoT) data from connected assets in a way that allows meaningful analysis leading to vital insights.
It can work with data from individual assets within a production line or scale to include enterprise-wide data streams.
The solution enables machine and production insights based on a seamless user experience leveraging contextualised data. It accelerates the realisation of common value-adding industrial IoT use cases by using ‘out-of-the-box’ intuitive capabilities. It can be configured and extended easily for solution specific customisation at scale.
Intelligent CIO spoke to Harshad Pingle, Product Manager for MindSphere, to find out more about the solution and how it is benefiting organisations.
Why is it important to put industrial IoT data in context?
Any business on a digitalisation journey knows that engaging with the industrial IoT is not as simple as adding some sensors and data collection capabilities. It’s not hard to drown in the sea of your industrial IoT data if you don’t have a solution that’s ready to accept it and put it to use. The structure of industrial IoT data is different than that of relational structured data and index-based semi-structured data that’s used in manufacturing and business operations.
Each piece of industrial IoT data comes with information about what physical property or state is being quantified, but it also contains contextual clues like when, over what duration, from which systems and how frequently the data was collected. The productivity and effectiveness of any analysis of industrial IoT data depends on how these data streams are processed, combined, compared, inserted and inferred.
A robust solution that can add relevant context information from other systems – customer relationship management (CRM), quality management (QMS), manufacturing execution (MES), enterprise resource planning (ERP), etc – to industrial IoT data can illuminate operational behaviour. Contextualised data makes analytics more effective and productive and enables data-driven decisions.
What’s the business value of putting industrial IoT data in context?
Contextualising your industrial IoT data is just one step toward making data-driven business decisions. When you combine data sets with the right analytics tools, you’ll be able to identify emerging trends and patterns that impact performance, efficiency and quality. Analytic tools that use contextualised industrial IoT data can help monitor the performance of individual assets and explore historical and up-to-the minute data about your operations.
They can speed up root-cause analysis, helping you to quickly identify changes and improvements to your operations. Insights from these analytics can also fuel continuous improvement initiatives within your organisation with the certainty that the data-driven changes will help your business meet its long-term goals.
What stops businesses from diving deeper into asset and performance data?
Businesses starting their digitalisation journey face a daunting task when they seek to contextualise industrial IoT data and build relevant, scalable analytics. Each step towards automation and digitalisation creates exponentially more data in a never-ending stream. Getting relevant data to teams within the company and making sure they have the tools to use it to its best advantage is another challenge.
Businesses also must consider how they will handle data collection, contextualisation and analysis when projects scale or products roll out. Many businesses make the mistake of evaluating either the technical value of industrial IoT data in context or its business value, not both. Consequently, homegrown data analysis tools developed in pilot stages may not be designed or resourced to scale to full-rate production or to other projects.
A related concern for many executives is whether their company has the deep IT skills required to build and maintain cloud-native IoT apps or the data science resources needed to uncover vital insights from the data collected. These executives might also ask themselves, ‘Do we really want to use our coding resources on this when they could be executing our core mission?’. This is especially true in times of business uncertainty when large expenditures are difficult to justify.
How does OI make it easier for businesses?
OI accelerates the realisation of common value-adding industrial IoT use cases by using ‘out-of-the-box’ solutions. It enables users to leverage their industrial IoT data to gain insights on common concerns like uptime and downtime, maintenance optimisation and performance, product output or performance, asset utilisation and availability, production process stability and yields.
The solution can be configured and extended easily for customisation and specific solutions at scale. It is customisable and scalable for a wide variety of industries, situations and stages of digitalisation. It can be easily extended with custom created applications.
What can businesses do right away to begin seeing results?
With OI, you can continuously monitor machine data and production key parameters of globally distributed production sites to get full and harmonised transparency on asset availability, conditions and anomalies. Custom-configured views show all the information available in one place. This can reduce the burden on site operators working with a high volume of assets. The solution lets you take and track actions to improve equipment effectiveness and availability by visually analysing all available data and detecting issues before they cause downtimes.
You can also build and monitor key performance indicators (KPIs), compare asset performance, and derive optimisation potentials. For a more customer and vertical-specific solution, you can tailor the solution with extension interfaces. In addition, you can leverage solution building blocks from third parties and business units that provide vertical-specific knowledge.
Click below to share this article